A steady spike in business has hit Eddie Kane Steel over the last couple of years. Plant manager Matt Knauff says 2024 is expected to be the best yet for the Masury company.
With just over 60 employees, the plant needs to add more staff as it continues to grow.
“We’re working on adding a third shift since we have an expansion coming,” Knauff said.
Positions that need to be filled include burn table, threading and saw operators, welders, galvanizing line, and general labor. Most employees work four, 10-hour shifts and have Friday through Sunday off.
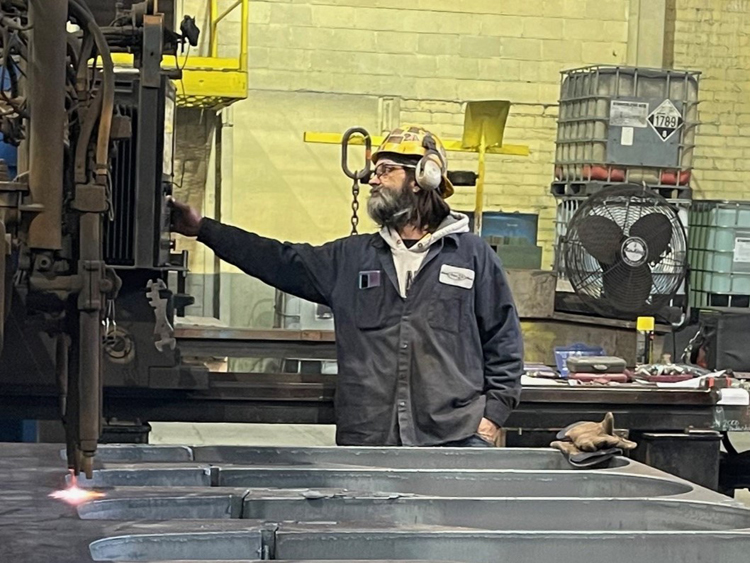
Branching out, building up customers
Eddie Kane’s local plant is among seven locations coast-to-coast that serve thousands of national customers. The distributor of flat plate steel also makes parts for trampolines, forklifts and dumpsters.
“We provide probably the most quality counterweights you can buy. We do about 2.5 million pounds per month of burned weight, 150 tons or more of flat plate steel and between 150 to 200 steel cages,” Knauff said.
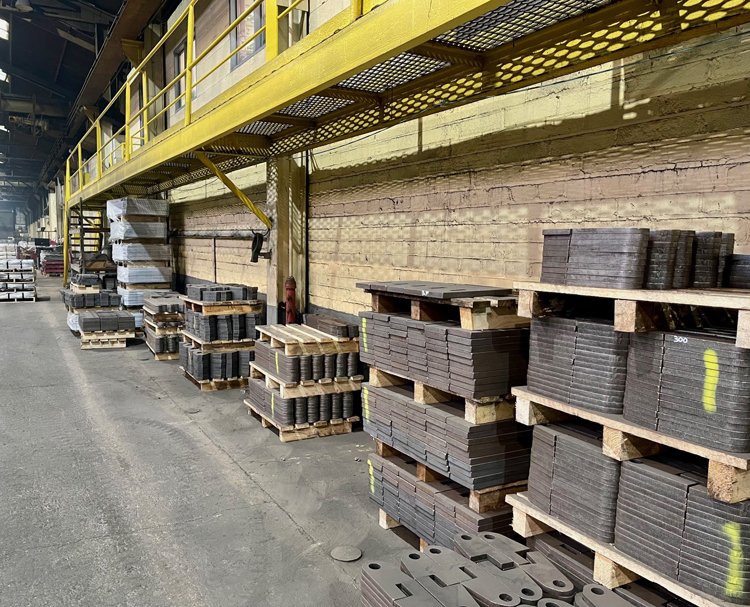
He noted that preparations are underway for the growth that’s expected this year.
“We put $2.5 million into the building. We’re redoing offices, some outside work and other various renovations.”
RB Steel, also in Masury, is Eddie Kane’s woman-owned branch, which is looking to expand. It specializes in anchor bolt cages for the construction industry, as well as telephone poles and power towers.
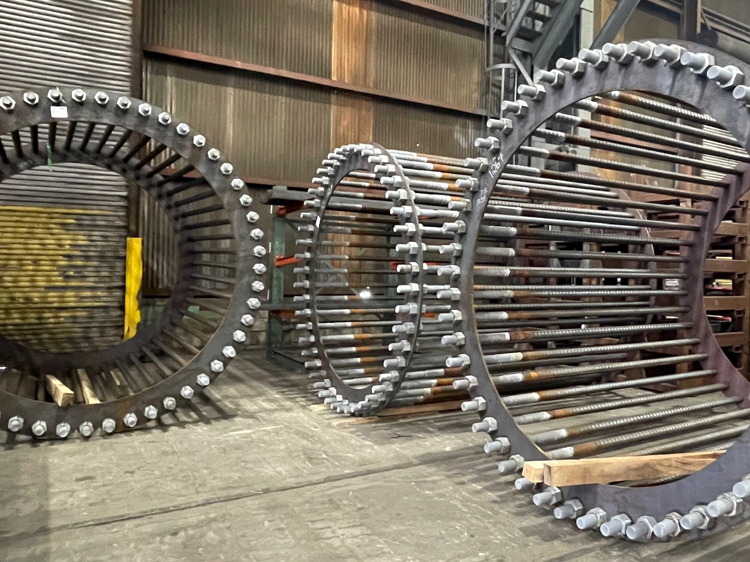
Connecting to MVMC
Knauff had a personal link to MVMC before joining the organization.
“I worked with Alex Hertzer when he was at ClarkDietrich for a while. Eddie Kane has been looking at ways to help bring people in and get more involved in the community. I knew Alex went to MVMC, so I gave him a call.”
What also attracted him to MVMC were the networking and best practice sharing opportunities.
“We like to help a lot of people who are trying to get their lives on track, so we’re interested in programs like WorkAdvance,” he said.
Eddie Kane supports diversity in the workplace, prioritizes hiring veterans and encourages women to apply for jobs.
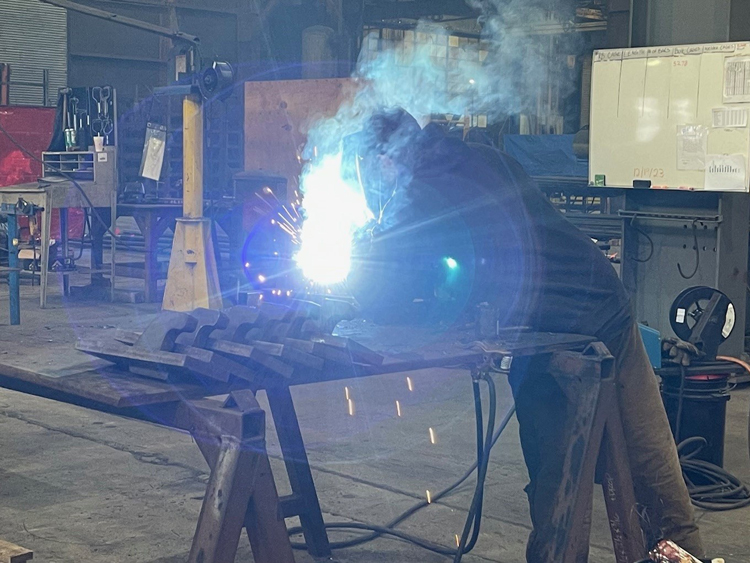
“We have female welders. We’ll help and train anyone who is willing to try, and we’ll even help people get jobs somewhere else if they aren’t a good fit here.”
Knauff says the company is implementing automated machines in 2024 to alleviate some of the physical labor for the manual grinders.
“It’s a difficult job, but this will make it easier for anyone to be able to do. It allows us to move employees around where gaps need to be filled.”
Although satisfying customers is top of mind, he says it’s just as important to keep employees safe, invest in them and be as supportive as possible.