If a list existed of people who are pillars of resilience and second chances, you would find Ta’Keyla Clayton’s name written on it. She credits WorkAdvance for giving her an opportunity to start over as an operator at Dinesol Plastics in Youngstown.
Clayton was working somewhere else when she heard about the program from a co-worker.
“He was saying good things about WorkAdvance, and he gave me the number for the career coach at the National Center for Urban Solutions, so I contacted him,” she said.
After giving about a month’s notice to her employer at the time, she joined the October 2023 cohort in Youngstown.
“My job before was sort of manufacturing, so I was familiar, but this seemed like a step towards growth and gaining more knowledge.”
She benefitted from the technical training, but Clayton was more surprised by her personal growth through WorkAdvance.
“The cohort always worked together and fed off each other when there were issues. We learned everybody’s weaknesses and strengths, and we could talk and help each other during the struggles. There was no judgment – just a lot of support.”
Facing and conquering challenges
After completing the program, she was hired at Dinesol in January 2024.
However, getting to that point was a bit rocky. A timing issue caused the first interview to be rescheduled. The second time, she showed up late. Reliable transportation remains her biggest challenge.
“I asked her what was going on, and I saw she needed a chance to help herself with everything she has going on. I just believed in her from the beginning,” said Krystal Schulz, HR manager, Dinesol Plastics.
Clayton’s mom gives her a ride to work most days but also battles serious health issues. That sometimes throws off Clayton’s schedule – mainly if she’s working on the weekend.
“I’ll usually just scramble to find a ride. As long as it’s not Sunday, I can take the bus,” she said.
Although she lives in Youngstown, a bus ride means an hour (or more) commute versus a 12-minute drive. It’s not affecting her work, though.
“Her attendance is great. She’s continuously making it happen. You’d never know there were any issues happening,” Schulz said.
Clayton admits the journey hasn’t been easy, but she’s grateful for the opportunity to prove herself.
“Krystal was understanding and worked with me, and I’m very considerate of that.”
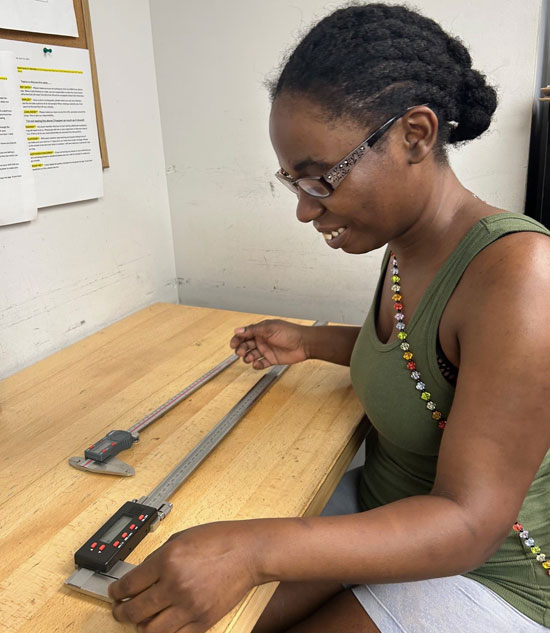
Growth with confidence
Aside from being an operator, she’s back up for quality assurance and training to be on the floor. Schulz says not many people get this far.
“I appreciate her, and I’m very proud. A lot of people give up, and don’t keep trying. I hope she sees herself the way I do. We hope to keep her for a long time.”
Clayton credits WorkAdvance for becoming more confident and a better communicator.
“The class had team building. You have to listen to people and step forward to learn how to work with others.”
Those skills will follow her to any job – even though she doesn’t plan to leave Dinesol anytime soon. She’s finding more financial freedom as well.
“I’m trying to get my own place and find something closer to the plant to make it easier to get back and forth to work.”
Despite that challenge, she says WorkAdvance is a good fit for anyone needing to improve their situation.
“Just try it. If you can’t find a job, or need a new job, you’ll get help through it and get to talk with people in different situations and circumstances. It helps you grow as a person,” Clayton said.