Fireline, Inc. in Youngstown realized it needed a better system to control mixers at the plant. The company was able to come up with a solution through Industry 4.0 concepts, assistance from the Youngstown Business Incubator and the organization MAGNET.
Fireline produces a wide range of slip-cast refractory ceramic shapes used to make parts in the aerospace industry. Manually controlled mixers are required in the process. Like many manufacturers, the company is dealing with being short-staffed, which can leave room for error due to employees taking on multiple tasks.
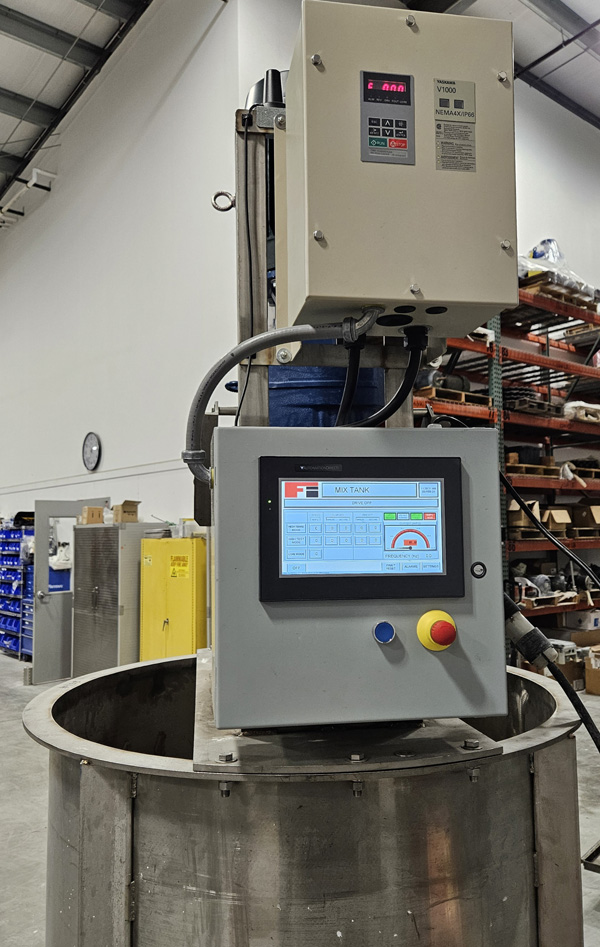
Automation to the rescue
Mark Peters is the director of engineering and has been with the company for more than 20 years. He says when a mixer is on high speed for too long and overheats, it’s a waste of material, time and costs a lot of money for repairs. That’s why Fireline wanted to develop a more automated system.
“We got an email notification from YBI about the funding for Industry 4.0 pilot projects and jumped on the opportunity,” Peters said.
Fireline then partnered with MAGNET and its engineers for about a year to develop a Wi-Fi connected mixer control system. It can be set on a certain recipe, run unattended and default to a slow speed when it would time out.
“MAGNET made it easy. Their engineers asked really good questions. We weren’t locked into specific equipment or systems. We figured out what was best for us.”
Fireline wanted to be able to monitor the mixing system, so specific data points are communicated to a central dashboard for the team to view.
“We spent a lot of time with this, gave them a mix tank for testing, and they came up with this system. It allows us to be proactive rather than reactive,” he said.
Ready for a trial run
The completed system was delivered to the company in November 2023. It’s being stored until it can be installed. Peters says other plant priorities have caused delays, but he’s hoping to start the trial run in the second quarter of 2024.
“We also need get people comfortable with the system before it’s implemented. Change can be hard, and there are specific ways this needs to run for monitoring.”
It will take about six months to determine its effectiveness. Now that Fireline knows the materials and design elements involved, the company plans to use the system on other mixers.
“Moving forward, this makes implementation easier. We now have the platform to eventually integrate other equipment,” Peters said. “MAGNET gave us a relative shortcut to getting it done. We would’ve used more resources and time doing the project on our own.”
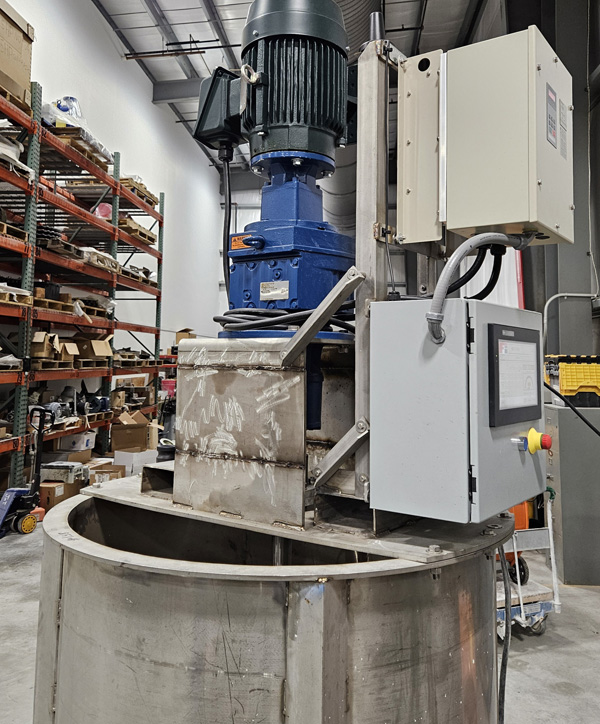
Benefits of implementing IIoT
He noted the company has also been using IIoT to monitor power and air compressors. Industry 4.0 is something he recommends to manufacturers that need to streamline production, save time and money.
“Technology pricing is down, and capabilities have increased. There are challenges, but the services MAGNET and YBI provide make it worthwhile. This is a time investment, but companies should take advantage. The money won’t be there forever.”
Peters says the total cost of the project was $35,000, but Fireline only paid $15,000 out-of-pocket. MAGNET also helped the company obtain some extra money through the Ohio Defense Community Grant – as it’s part of the defense supply chain.
“It’s not a one-size-fits-all approach. But when you look at an IIoT system like ours, this solves all the issues. The payback is immediate on something like this.”
YBI funding for Industry 4.0 pilot projects runs through 2024. Contact Daniel Longo or Stephanie Gaffney to begin an assessment or for more information.